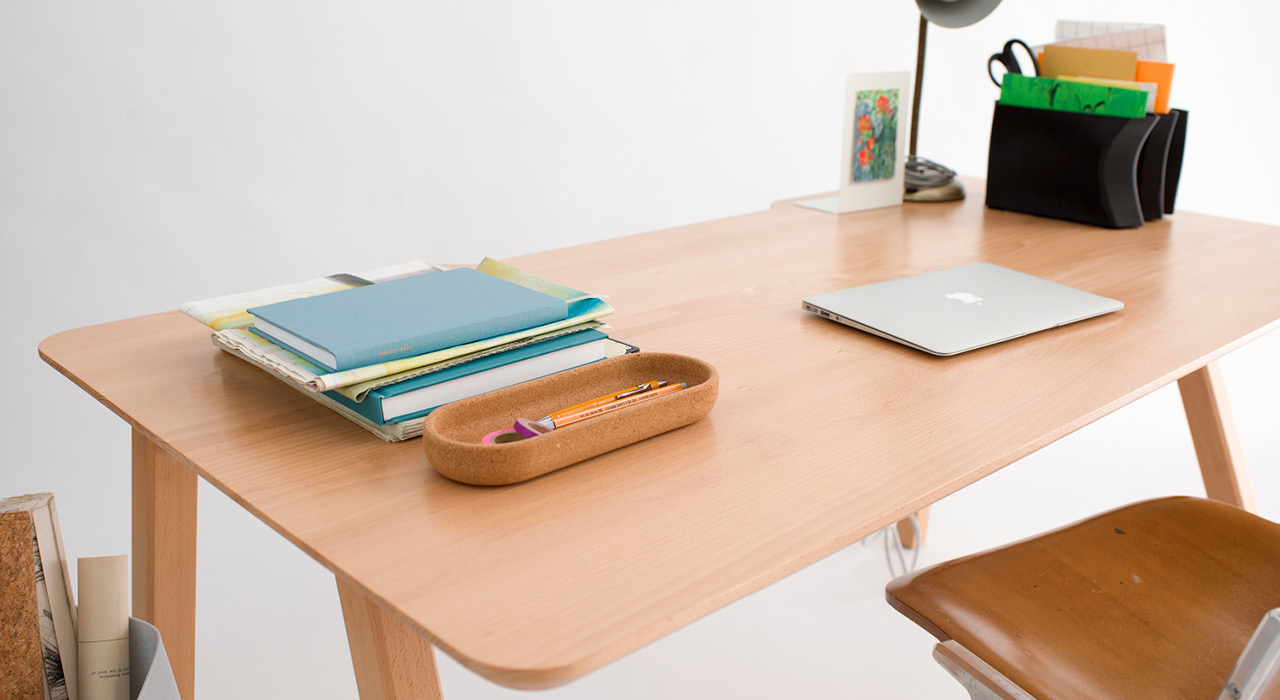
Model No. provides bespoke furniture with short-lead times, by using the latest 3D-printing technology. 3D-printed items are traditionally made with petroleum-based plastics, which is great for customization, but bad for the environment. So Model No. uses biopolymers and plant-based resins instead. These materials are sourced from the remains of food crops, reducing waste and providing a purpose for otherwise unused materials. They supplement the 3D-printed elements with locally sourced, reclaimed and FSC-certified wood and recyclable materials like steel and aluminum. And because each item is made to order, inventory waste is eliminated, too. We spoke to co-founder and CTO, Jeffrey McGrew, to find out more…
Tell me a little bit about your childhood, education and background in terms of how you first became interested in creativity, design and sustainability.
I’m actually a licensed architect, and prior to Model No. I was running a very sustainably-minded creative design-build firm. Growing up in Wyoming, and then moving west, I’ve always been obsessed with empowerment via new technologies to make more interesting and sustainable things. Thankfully there’s been a big push in the construction industry to become more sustainable, but in order for that to fully happen, we also need better options for what we put into those buildings. And all these wonderful new fabrication technologies really open up what’s possible to do creatively. So it’s a perfect match!
How would you describe this project?
Model No. is revolutionizing how furnishings are designed, produced and sold. Our distinctive approach provides custom, sustainable products with accessible price points that are created on-demand by consumers. Made domestically in localized highly-automated factories, all our furnishings are artfully crafted from sustainably sourced materials, such as upcycled food waste, and produced using the latest eco-friendly tech, including 3D-printing. With just a few clicks online, consumers customize products and they are made to order and delivered in a few weeks, eliminating long wait times and wasteful inventory.
What inspired this project?
The current furniture market is outdated, so there is a need for companies to push the industry forward. The industry consists of items that are mass-produced out of the country, with little original design or customization ability, shipped very long distances, and made from materials that typically are not very sustainable or eco-friendly. This all contributes to large carbon emissions and overall waste. With these pain points in mind, I founded Model No. with Jillian Northrop and Vani Khosla to solve these problems and reimagine how you can access sustainable, customizable, artfully designed furnishings.
What waste (and other) materials are you using, how did you select those particular materials and how do you source them?
Through the use of agricultural waste from corn husks, sugar cane and sugar beet as materials, Model No. minimizes carbon emissions and toxic byproducts. We also use reclaimed and certified sustainably harvested wood for products such as tabletops, coffee tables bases and our headphones stands, to upcycle wood products or utilize leftover wood. So whether a product is all 3D-printed, or all wood, or some combination of the two, it’s always as sustainable as we can possibly make it. In order to reduce our carbon footprint caused by shipping products across the world, we source 95% of our materials from farms within the U.S. These include Jamplast (Raw PLA), Spectra (Coloring services for the PLA), Techmere (Raw PLA), Moore Newton (Hardwoods), and Aura Hardwoods (Hardwoods and plywoods).
When did you first become interested in using waste as raw material and what motivated this decision?
As we explored using large-scale industrial 3D-printing for producing furniture, it became apparent that we could use resins that originated from food waste and were compostable. We’ve since developed the ability to recycle this resin as well, so that we can recycle our own products and use them to produce new products. We’d always intended to make the best sustainable furniture possible, pieces that are not only great looking and high-performance, but that would also be healthy to be around for both our customers and our employees. So when we saw it was possible, we really committed to this direction.
What processes does the material have to undergo to become the finished product?
We grind food waste – such as corn husks, sugar canes, sugar beets and cassava – into a PLA – Polylactic Acid – for it to be 3D-printed. For CNC fabrication, we utilize waste and by-products such as reclaimed wood, as well as sustainably harvested woods, which can be shaved down and repurposed for items such as Model No.’s tabletops.
What happens to your products at the end of their life – can they go back into the circular economy?
We plan to add recycling facilities in these spaces in order to take back used items. Hinting at the company’s name ‘Model No.’, each product has its own individual model number, making it easy to identify the type of material that the product was built with and the year it was manufactured so it can then be broken down to raw materials to be repurposed through 3D-printing.
How did you feel the first time you saw the transformation from waste material to product/prototype?
Ironically while I was obviously elated that we were able to do it, we also then immediately broke the first items in the rigorous testing we do to ensure our products meet the highest quality standards! It was when we figured out how to then fully recycle those broken products and re-use the resin that I fell completely in love with the whole process.
How have people reacted to this project?
People have reacted very positively to our commitment to sustainability, design and on-demand customization. We have been recognized as an industry leader in the media and have had several companies reach out for collaboration. It is our hope that we can inspire not only consumers to shop sustainably, but also encourage other companies to follow suit.
How do you feel opinions towards waste as a raw material are changing?
With natural disasters occurring more frequently – an obvious sign of global warming – there is a growing conscientiousness to do more to protect the environment. I think that people and companies are seeing the value in upcycling as recognition of the need for sustainability continues to become more and more apparent.
What do you think the future holds for waste as a raw material?
There is much work to be done to develop our ability to utilize waste as a raw material. We are very proud of the work we have done so far in turning waste into items that consumers can enjoy on a daily basis; however, we also recognize that more needs to be done. We hope to continue to discover how different types of waste can be upcycled and hope to inspire other industries to do the same.